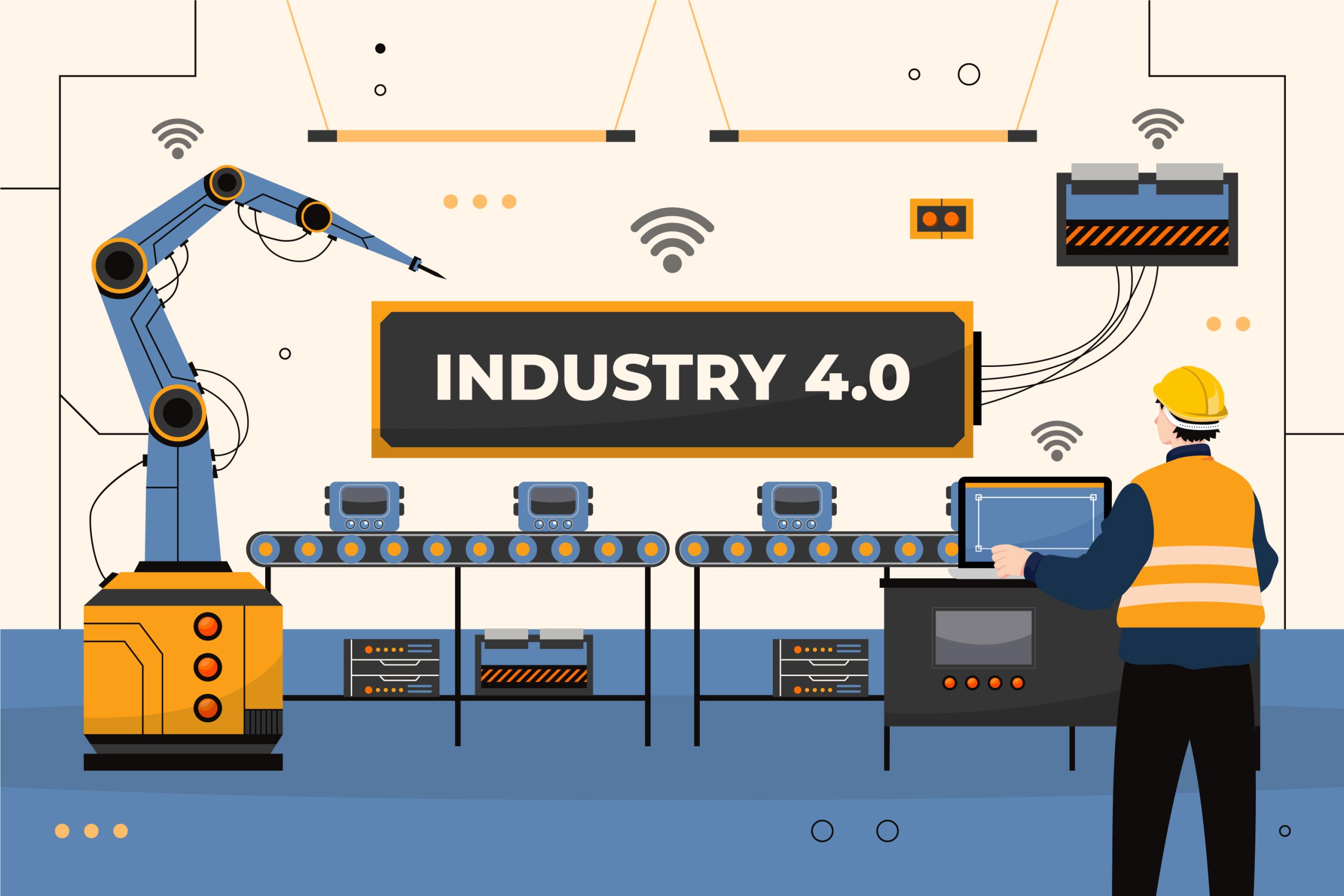
The term “industry 4.0,” or “fourth industrial revolution,” refers to a new stage of the industrial era. It is typified by incorporating cutting-edge technologies into production procedures, creating “smart factories” with autonomous, networked machines and systems. This revolution creates intelligent, networked production environments by utilizing cloud computing, artificial intelligence (AI), cyber-physical systems, and the Internet of Things (IoT).
Let’s see how Industry 4.0 technologies are changing manufacturing.
The adoption of Industry 4.0 technologies is transforming manufacturing in profound ways:
- Increased Efficiency
Automation and AI
- Real-time Monitoring: Automated systems and AI algorithms continuously monitor production processes, collecting and analyzing data to optimize performance. This real-time monitoring helps identify bottlenecks and inefficiencies, allowing for immediate corrective actions.
- Optimization: AI-driven analytics optimize resource usage, energy consumption, and process parameters, reducing waste and improving overall efficiency. This leads to lower production costs and higher output.
- Enhanced Flexibility
Smart Factories
- Adaptability: Smart factories equipped with interconnected machines and flexible production lines can quickly adjust to changes in product demand and customization requests. This adaptability enables manufacturers to produce a wide variety of products without significant downtime or retooling.
- Agility: Advanced manufacturing systems can seamlessly switch between different production tasks, allowing for just-in-time manufacturing and rapid response to market changes.
- Improved Quality Control
Advanced Sensors and Analytics
- Continuous Monitoring: Advanced sensors embedded in production equipment continuously monitor product quality, ensuring that each item meets specified standards. These sensors detect deviations in real time, allowing for immediate corrective actions.
- Early Defect Detection: By analyzing data from multiple sources, AI and machine learning algorithms can identify patterns that indicate potential defects, enabling early intervention and reducing the likelihood of defective products reaching customers.
- Supply Chain Integration
- Seamless Communication: IoT devices and cloud-based platforms enable real-time data exchange and communication across the supply chain. This integration ensures that all stakeholders, from suppliers to distributors, have access to up-to-date information.
- Improved Transparency: Enhanced visibility into the supply chain helps manufacturers track the movement of raw materials, components, and finished products. This transparency reduces delays, improves inventory management, and ensures timely delivery.
- Predictive Maintenance
Sensor-equipped Machines
- Condition Monitoring: Machines equipped with IoT sensors monitor their own performance and condition. These sensors collect data on factors such as temperature, vibration, and usage patterns.
- Predictive Analytics: AI-driven predictive analytics analyze this data to predict when maintenance is needed, allowing for scheduled maintenance before a breakdown occurs. This proactive approach minimizes unexpected downtime, extends equipment lifespan, and reduces maintenance costs.
Challenges and Considerations
While Industry 4.0 offers tremendous opportunities, it also presents challenges that must be addressed:
- Cybersecurity Risks: Increased connectivity exposes manufacturing systems to cyber threats. Robust cybersecurity measures are essential to protect sensitive data and prevent disruptions.
- Skill Gaps: The shift towards digital technologies requires upskilling and reskilling the workforce. Investment in training programs is crucial to equip employees with the necessary competencies.
- Integration Complexity: Integrating diverse technologies and legacy systems into cohesive Industry 4.0 ecosystems can be complex and costly. Compatibility standards and strategic planning are essential for successful implementation.
Time to time transformation: Historical Context for Industry 4.0
1.First Industrial Revolution (late 18th to early 19th century)
Key Characteristics:
- Steam Power: Introduction of the steam engine revolutionized production.
- Mechanization: Innovations in textile manufacturing with machines like the spinning jenny and power loom.
- Iron and Coal: Advances in iron production and coal use fueled growth.
Impact:
- Economic Growth: Increased productivity and economic output.
- Urbanization: Shift from rural to urban living for factory jobs.
- Societal Changes: Emergence of new social classes.
2.Second Industrial Revolution (late 19th to early 20th century)
Key Characteristics:
- Electricity: Enabled safer, more efficient factories.
- Mass Production: Assembly lines, exemplified by Henry Ford’s automotive production.
- New Materials and Chemicals: Development of steel and synthetic chemicals.
Impact:
- Global Trade: Enhanced transportation and communication.
- Labor Movements: Growth of unions and advocacy for workers’ rights.
- Technological Advancements: Progress in various industries.
3.Third Industrial Revolution (mid-20th century)
Key Characteristics:
- Electronics and Computers: Rise of transistors, integrated circuits, and computers.
- Automation: Introduction of programmable logic controllers (PLCs) and robotics.
- Digital Revolution: Emergence of the internet and personal computing.
Impact:
- Information Age: Shift towards knowledge-based economies.
- Globalization: Increased international market integration.
- Workforce Changes: Demand for technical and knowledge-based skills.
4.Fourth Industrial Revolution (21st century)
Key Characteristics:
- Fusion of Technologies: Integration of IoT, AI, and advanced robotics.
- Smart Manufacturing: Real-time data collection and analysis.
- Advanced Robotics: Autonomous robots with AI capabilities.
- Additive Manufacturing: 3D printing for customized production.
- Biotechnology and Genomics: Breakthroughs in medicine, agriculture, and sustainability.
Impact:
- Increased Efficiency: Enhanced productivity and reduced downtime.
- Customization: Ability to produce on demand and adapt to market changes.
- Workforce Transformation: Growing demand for digital and tech skills.
- Ethical Challenges: Issues like data privacy, cyber security, and job displacement.
What Technologies is Driving Industry 4.0?
Several key technologies underpin Industry 4.0:
- Internet of Things (IoT): The Internet of Things (IoT) is a network of interconnected devices that collect and exchange data over the internet, enabling automation and intelligent interaction without human intervention.
- Artificial Intelligence (AI) and Machine Learning (ML): Artificial Intelligence (AI) is the simulation of human intelligence in machines, enabling them to perform tasks like reasoning, learning, and problem-solving. Machine Learning (ML) is a subset of AI that involves training algorithms on data so they can learn patterns and make predictions or decisions without being explicitly programmed.
- Big Data and Analytics: Big Data refers to extremely large datasets that are complex and difficult to process using traditional methods. Analytics involves examining these datasets to uncover patterns, trends, and insights.
- Robotics and Automation: Robotics and Automation in manufacturing involve using robots and automated systems to perform tasks, increasing efficiency, precision, and productivity while reducing human intervention.
- Augmented Reality (AR) and Virtual Reality (VR): Providing immersive training experiences and aiding in complex assembly tasks.
- Cybersecurity: Cybersecurity in the context of the industrial revolution involves protecting industrial systems and networks from cyber threats, ensuring the safety and integrity of data and operations.
Conclusion
Industry 4.0 is revolutionizing manufacturing by integrating advanced technologies that enhance efficiency, flexibility, and quality. From its historical roots in the steam-powered First Industrial Revolution to today’s interconnected smart factories, each phase of industrial development has built upon the last.
With the continued advancement of technologies like IoT, AI, and cloud computing, the Fourth Industrial Revolution promises to drive unprecedented levels of innovation and productivity in the manufacturing sector.
Embracing these technologies enables manufacturers to achieve new levels of efficiency, customization, and competitiveness in the global marketplace.
No comment yet, add your voice below!