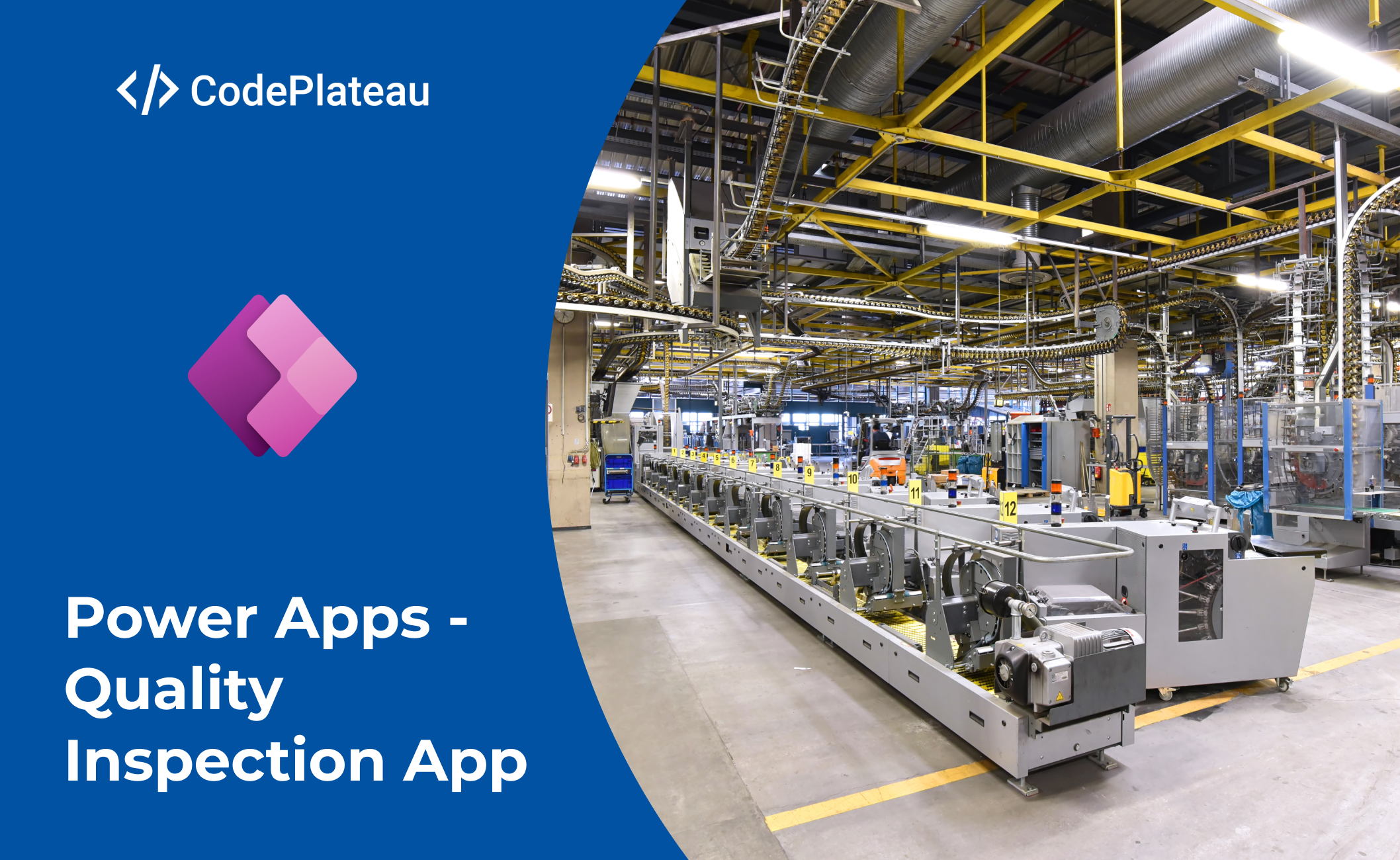
The manufacturing industry faces numerous challenges in maintaining quality inspection and tracking key performance indicators (KPIs). Traditional paper-based procedures are inefficient and prone to mistakes and delays. Manual data input frequently results in errors, missing papers, and a lack of real-time data visibility.
Furthermore, the time-consuming process of gathering and evaluating paper records hampers timely decision-making and corrective action. Being unable to easily access previous data restricts the detection of trends and root causes, making retracing a considerable challenge.
Necessity of Power Apps:
The inability to quickly access historical data complicates the identification of trends and root causes, making backtracking a serious issue.
The need for a digital transformation is evident, and Power Apps offers a compelling solution. Power Apps, part of the Microsoft Power Platform, enables businesses to create custom applications with minimal coding, making it ideal for developing a comprehensive Quality Inspection App that can digitize and streamline the inspection process.
Power Apps: A Cost-Effective Solution:
One of the significant advantages of using Power Apps for quality inspection and back tracing is its cost-effectiveness.
Developing applications using Power Apps is significantly cheaper compared to traditional app development for Android and iOS.
Power Apps allows manufacturers to design customized applications without requiring extensive coding experience or a big development team. This low-code platform eliminates the need for a large initial investment, making it affordable for businesses of all sizes.
Rapid Development and Deployment:
In addition to being cost-effective, Power Apps offers a remarkably quick turnaround time for app development.
Traditional app development might require months of design, coding, testing, and release. In contrast, Power Apps enables the quick development and deployment of apps, frequently within few weeks.
This speed is critical for manufacturers that must respond quickly to changing needs and continuously improve their quality control methods.
Let’s take a deep dive in Quality Inspection App:
->Creating a Quality Inspection App with Power Apps requires a few steps:
First, configuring Power Apps is simple. Users may create a new project, get to know the interface, and use the platform’s core functions.
Designing the user interface is critical to ensure that examiners can efficiently login data. This includes building user-friendly data entry forms and tailoring the interface to the inspection team’s specific requirements. Integrating data sources is another critical step.
->Data Connectivity:
Power Apps seamlessly connects with various data sources such as SharePoint, SQL Server, and Excel, enabling real-time data updates and ensuring that all inspection data is centralized and accessible.
->Downtime Reduction:
Automation of operations through workflows utilizing Power Automate improves efficiency. Workflows can automate quality checks and approval procedures, allowing for more prompt inspections and follow-ups. These automated techniques eliminate manual involvement, reduce mistakes, and shorten the inspection cycle.
Safety & Quality Control:
Safety & Quality Control, KPI such as defect rates, inspection pass rates, and corrective actions are essential. Digital checklists and the ability to capture photos of defects streamline the inspection process.
Data analysis tools within Power Apps allow for the visualization of trends and identification of improvement areas.
Backtracking quality issues becomes straightforward as defects can be traced back to specific production stages and responsible personnel, enhancing accountability and corrective action effectiveness.
The Challenge of Back Tracing in Manufacturing:
One of the critical components of quality control in manufacturing is the ability to backtrace a product’s history.
Back tracing is the process of tracking a product from raw ingredients to final production. This procedure is critical for determining the underlying cause of any quality issues that develop and guaranteeing that all goods satisfy the appropriate standards.
However, back tracing can be a considerable challenge due to the complexity of manufacturing processes.
Each product may pass through numerous stages, involving different machines, operators, and materials. Traditional methods of back tracing rely on paper records and manual data entry, which can be time-consuming and prone to errors.
This complexity makes it difficult to quickly and accurately identify the source of any issues.
Backtracking made easy:
Implementing backtracking for KPI’s in Power Apps is crucial for continuous improvement. By interlinking data entries, such as linking incidents to specific inspections, and setting up audit trails to track changes and actions taken, businesses can ensure comprehensive traceability.
Power BI can be used to generate comprehensive visualizations that enable retracing and provide insights that lead to better decision-making and accountability.
Real-world case studies demonstrate the effectiveness of backtracking in terms of compliance and continuous improvement.
Conclusion:
In conclusion, a Quality Inspection App designed using Power Apps has several advantages, including increased efficiency, accuracy, and traceability.
The digital transformation journey can result in significant changes in how industrial processes are controlled. As the industry evolves, potential future enhancements like AI integration and predictive analytics will further boost the capabilities of such apps.
Share your thoughts with us, we’d love to hear from you. If you have any questions or would like to know more about our Power Apps services, please feel free to contact us.
No comment yet, add your voice below!